Computerized Maintenance Management System (CMMS)
Key Features & Benefits
-
Speedy notifications of major breakdowns
-
Prompt activation of maintenance team
-
Maintenance ‘backlog’ by workstation auto populated
-
Minor repairs captured and cataloged
-
Spare parts inventory simplified
-
Our parts-finder labels part to workstation
-
Easily schedule machine downtime
-
Hours/materials used embedded with every maintenance call
-
Easy ‘follow up’ maintenance planning
-
Preventative maintenance work aids included
-
Machine readiness at a glance
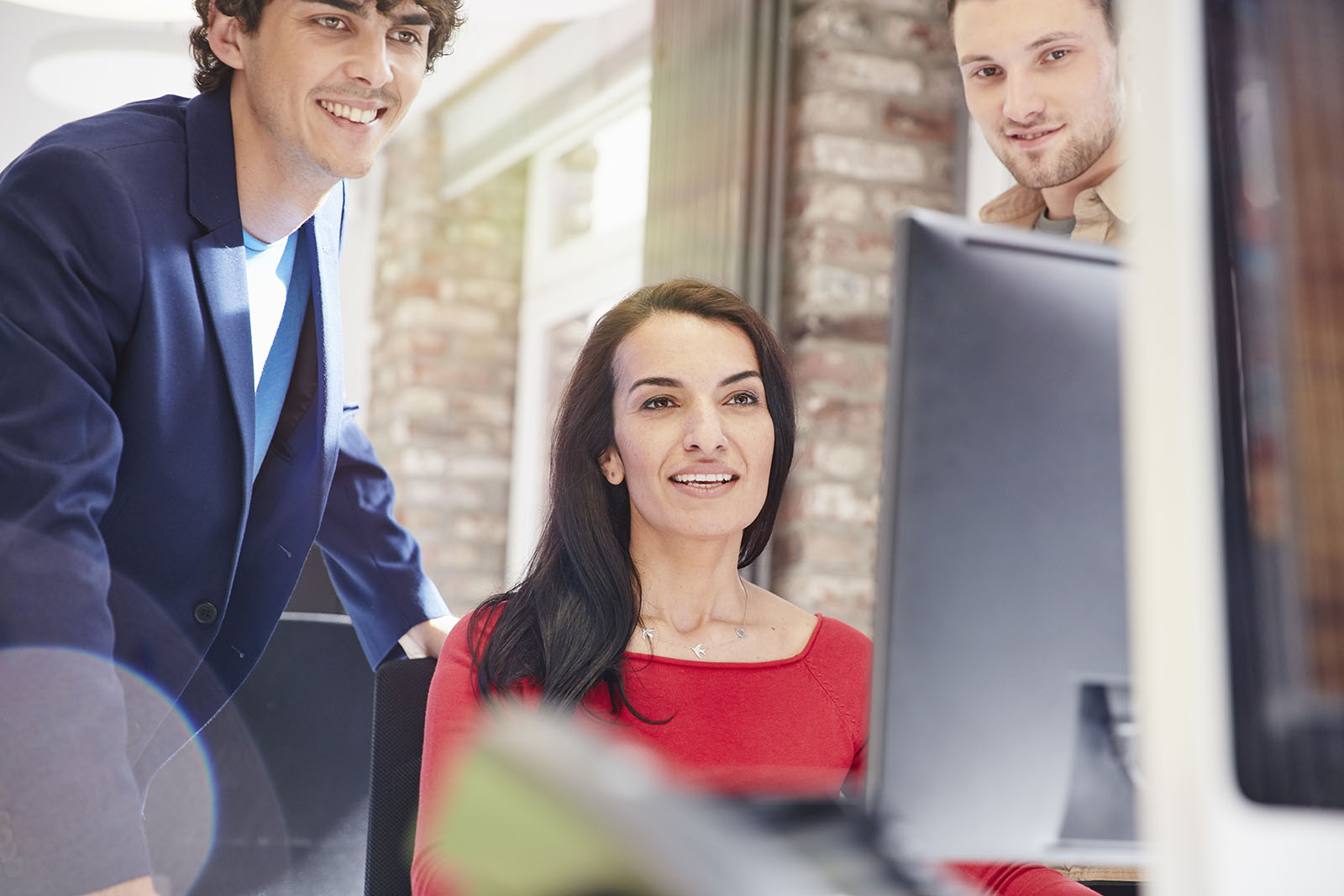
Summary of Key Deliverables for the Maintenance Program
Hear How Our Customers Have Grown A Hundred Fold
See What PolyPM Can Do For You
The only no excuses, profit-driven, cost-cutting, all-in-one system you will ever need for your apparel business.
Tell us who you are, what you want and we'll tell how PolyPM can help.
Office Address
Office Hours
Monday - Friday 8AM to 5PM Eastern Time